Upstand Boards
Thermal insulation and protection to upstands parapet walls on flat roofs, typically inverted roof applications.
PRODUCT
AIM Insulated Upstand Boards are manufactured from a variety of insulation materials including the leading brands of extruded polystyrene (XPS) foam or Stone Wool insulation, factory bonded to our external grade high impact fibre cement facing board.
APPLICATIONS
AIM Insulated Upstand Boards are used to provide
thermal insulation to upstands and parapet walls in
flat roof constructions, typically inverted roof systems.
The primary function is to insulate the parapet
upstand and prevent cold bridging to the internal
envelope of the building.
AIM Upstand Boards are designed to provide a tough,
weather and impact resistant finish which can be
decorated as required.
A limited-combustibility A2-s1,d0 stone wool option is
available for buildings over 11m high.
FEATURES
- A range of insulation substrates to meet the requirements of the project.
- A range of thermal performances to suit the requirements of the project.
- A Euroclass A2-s1,d0 stone wool based option is available.
- Pre-decorated and through coloured facing boards are available.
- Standard sizes as well as custom dimension product available.
BENEFITS
- Low thermal conductivity helps provide a thermal break at the base of upstands and perimeter walls of a flat roof.
- Provides a robust substrate for decoration as required.
- Compatible with most flat roof waterproofing systems.
- Highly weather resistant and suitable for long term weather exposure.
- Wide range of sizes available to give flexibility of installation.
- Easy to install
- Euroclass A2-s1,d0 option available for buildings over 11m high.
- Pre-cut boards available to suit specific parapet heights.
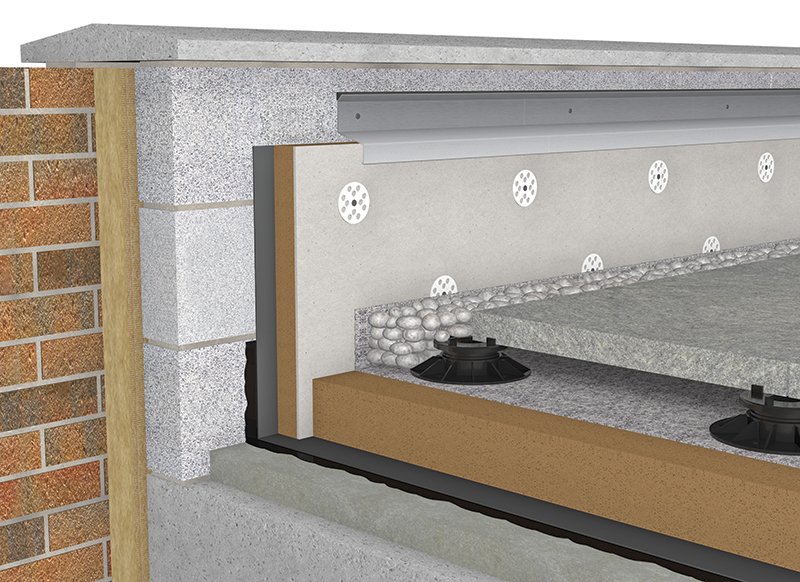
Example product installation schematic using materials by others
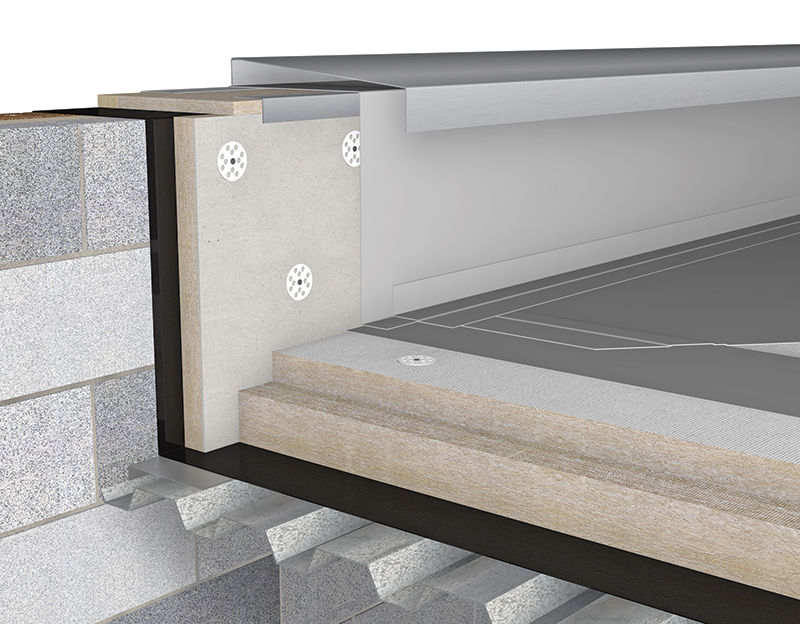
PHYSICAL INFORMATION
- 1200mm long x 600mm wide
- Insulation 50mm thick
- High Impact facing board = 6mm thick
- Overall thickness of 56mm
- Non-standard thicknesses and sheet sizes also available
- Also available pre-cut to specific heights.
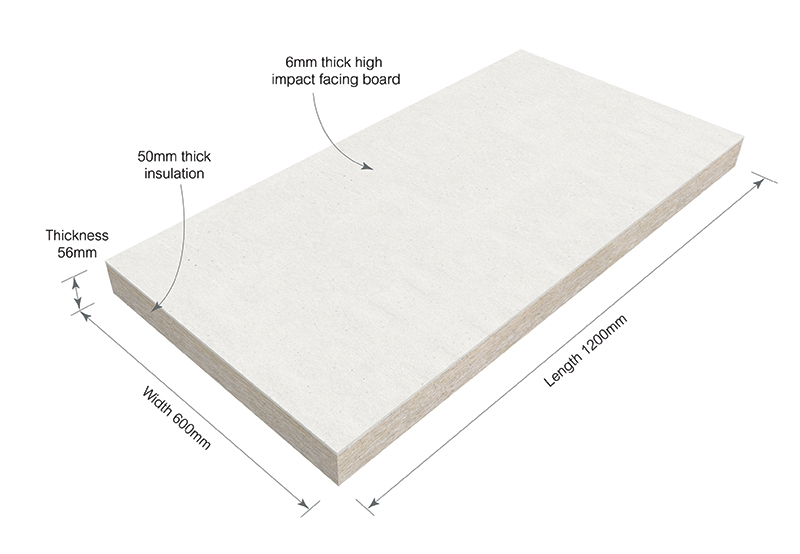
AS STANDARD
The standard board configuration is 1200 x 600 x 50mm insulation faced with a 6mm fibre cement board.
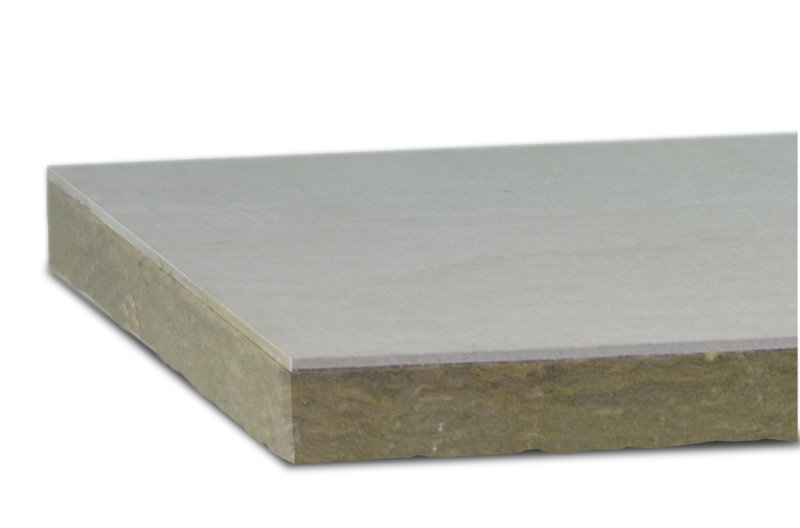
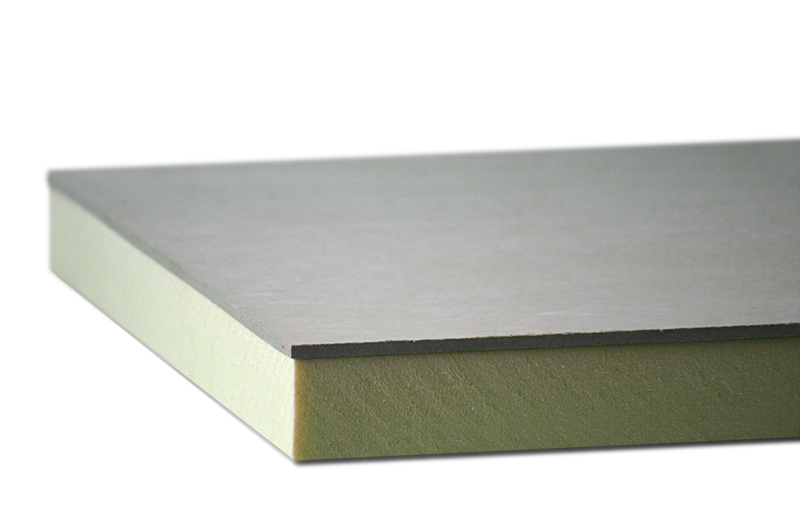
PACKAGING
AIM Upstand Boards are stretch wrapped onto wooden pallets with a showerproof polythene pallet cover and high quality edge protectors.
OPTIONS
AIM is able to manufacture the Upstand board using
a variety of different thermal insulation (XPS and stone
wool being the most common materials).
We are also able to manufacture boards up to
2400 x 1200mm and in a wide range of thicknesses
to suit the project.
TECHNICAL INFORMATION
Thermal Performance
Varies according to the insulation used.
Generally in the range of 0.030 to 0.040 W/mK
The facing board has a thermal resistance of
0.30W/mK
Compressive Strength
The compressive strength of the insulation varies
according to the insulation substrate used. Details
available on request.
The facing board is highly resistant to impact damage
and offers an extremely robust finish.
Decoration
Where required the facing board may be painted
without any special priming using an alkali resistant
paint or emulsion.
Two coats of paint will usually give a satisfactory finish.
Suitable paints are: Gloss Paints, Acrylics, Chlorinated
rubber, Epoxy, PVA, PVC, Polyurethane and silicate.
The standard facing board is not intended to provide a final architectural/aesthetic finish as the cementitious
facing may vary in colour from batch to batch.
Pre-finished and through coloured facing boards are
available upon request.
NOTE: Decoration and the application of paint may
impact on the overall fire classification / combustibility
of the product.
TEST REPORTS
Classification of reaction to fire performance in accordance with EN 13501-1 Report Number WF514062 (applies stone wool version only).
Reaction To Fire
AIM Upstand Boards backed with Stone Wool
insulation achieve Euroclass A2-s1,d0.
Other insulation variants will not meet the
requirements for limited-combustibility.
Water Repellence
XPS insulation is highly resistant to absorption of water so the XPS Upstand Board variants are the preferred choice where this could be of concern. Should a Stone Wool backed Upstand board be required, for instances where a limited-combustibility construction is specified, water is unlikely to penetrate to a depth greater than a few mm into the body of Rockwool insulation unless the product is held in water and the air forced out. Subsequent to total immersion testing in accordance with BS 2972, Rockwool products will typically absorb less than 2% water by volume.
Weather resistance
The facing board is a fully external grade, freeze resistant.
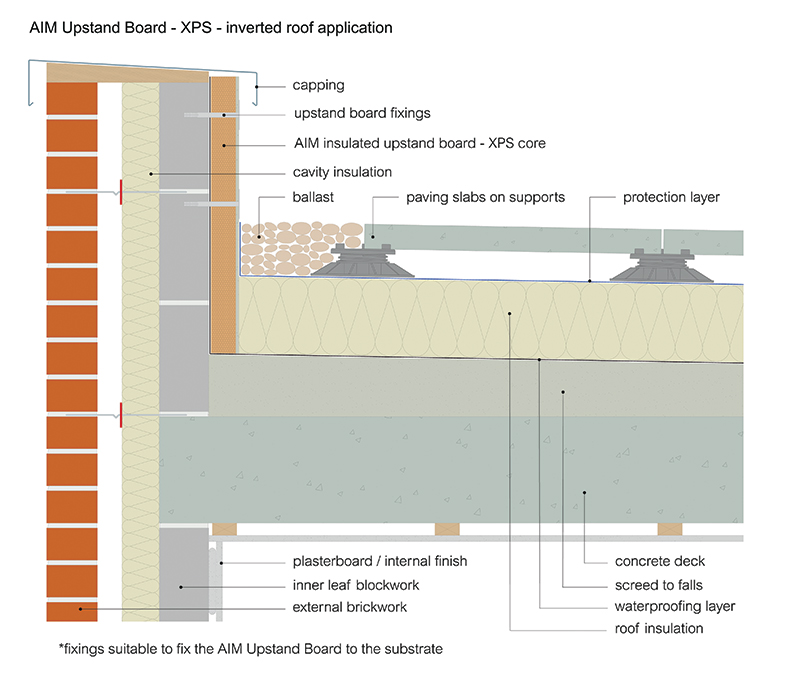
AIM Upstand Board - XPS - Inverted roof application
INSTALLATION GUIDELINES
Installation will vary according to the roof system
which is being used. For specific guidance, please
refer to the relevant waterproofing system holder.
AIM Upstand boards are supplied as 1200 x 600mm
boards as standard and can be used either way up or
cut to size as required.
The boards should be cut to size using a TCT saw (an
FFP3 face mask is advised to guard against dust).
The Upstand Boards should be installed before the
horizontal insulation which is then used to hold the
base of the Upstand Board in place.
The board should be fixed directly to the upstand
wall using through fixings. Fixing centres should not
exceed 600mm. Fixings should be positioned at least
50mm from the top of the facing board, but should
not exceed 200mm.
In the event that a roof deck is not supporting the
bottom of the board, additional through mechanical
fixings should be used to compensate.
The mechanical fixings used should be appropriate for
the depth of insulation and type of substrate in which
the fixing is to be made.
The screws should be installed with a controllable
speed screw gun and not overdriven, to prevent
undue compression of the insulation backing. We
suggest avoiding any counter sunk fixings and
hammer fixings
The fixing pattern is dependent on the type of fixings
used and the substrate in which the fixing is to be
secured.
Please seek advice from your nominated fixing
supplier
Mechanical Fixings:
AIM recommends a pan head fixing suitable for the
substrate or similar approved when installing this
product.
Ensure that the fixings are a minimum of 30mm longer
than the overall thickness of the board.
When installed, provided that the top surface is
protected by a sill or cover, the AIM Upstand Board
is suitable for long term exposure - for example when
used in conjunction with an inverted roof system.
Where the High Impact Soffit Liner Board needs to
be cut to size, a skill saw fitted with TCT blade and
suitable dust extraction should be used along with the
appropriate personal protective equipment.
ITEMS REQUIRED FOR INSTALLATION
- PPE abrasion resistant gloves
- PPE impact resistant goggles
- RPE dust mask - FFP3
- Skill Saw and TCT blade
STORAGE
Products are supplied on wooden pallets with edge protection and a shower proof hood. Products should be stored away from the elements until ready for installation.
MAINTENANCE
This product does not contain moving parts and, if undisturbed, requires no routine inspections or maintenance.
DURABILITY
AIM Upstand Boards are chemically inert, will not
sustain vermin and do not encourage the growth of
rot, fungi, moulds or bacteria.
They are compatible with all normal building materials.
They do not degrade under the usual anticipated
conditions found in buildings and will perform
effectively for the life of the building.
HEALTH & SAFETY
Insulation products supplied by AIM are considered
to be inert articles and as such are exempt from
requirements to provide a Safety Data Sheet.
When dry working (cutting/drilling/screwing) the facing
board dust protection must be considered.
Product Safety and Handling Information Sheets are
available covering the various insulants and facing
board used.
ENVIRONMENT
Stonewool global warming potential = zero
XPS Foam Global Warming Potential = >5
ORDERING
To order this product the following information will be
required:
- Dimensions of the required boards
- Approximate quantity
- Thickness required
- Delivery location
All AIM fire barriers are made to order. Products are
typically supplied in seven to ten working days but
lead times may vary depending on existing factory
commitments.
There is no minimum order quantity or value although
small orders may attract transport surcharges.
TECHNICAL SUPPORT
Technical Support is available from our experienced sales team on 01293 582 400 or [email protected]
Our Partners & Affiliates

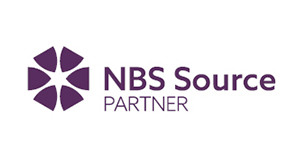
AIM are partners with NBS. Our products can be found on NBS Source and have been authored to NBS specification standards and have both CAWS and Uniclass 2015 classifications.